Die Spritzenpumpe bietet aufgrund des volumetrischen Förderprinzips und der minimierten Pulsation enorme Vorteile für mikrofluidische Anwendungen. Sie hat aber auch einen großen Nachteil gegenüber anderen Pumpen: Die Förderung endet naturgemäß, sobald die Spritze leer ist. Deshalb kommt die Spritzenpumpe vermehrt zum Einsatz bei Anwendungen, wo dies keine Rolle spielt, weil der Prozess pausiert und die Spritze wieder befüllt werden kann, wie z.B. das Füllen einzelner Kavitäten beim Pipettieren.
Bei vielen Anwendungen – vor allem in der Flow Chemie – wäre eine Unterbrechung nicht möglich, da diese den stabilen Zustand (steady state) stören würde, der sich bereits zu Beginn des Prozesses durch den Fluss der Eluenten (miteinander reagierende Chemikalien) eingestellt hat.
Dieses Problem lässt sich lösen, indem man pro Dosierkanal zwei Spritzenpumpen einsetzt, die alternierend arbeiten. Das heißt, wenn die erste Spritze leer ist, übernimmt die zweite Spritze die Förderung, während mittels eines 3/2-Wege Ventils die erste Pumpe aus einem Reservoir wieder befüllt wird. Anschließend übernimmt die erste Spritze wieder die Förderung, und die zweite Spritze wird erneut befüllt.
Um keine harten Schaltimpulse zu erzeugen, müssen beim Umschalten von der einen auf die andere Pumpe, statt des abrupten Stoppens, flachere Beschleunigungs- und Bremsrampen (Crossflow) gefahren werden. Bei Anwendungen unter höheren Drücken reicht das allerdings nicht aus, um sämtliche Druck- bzw. Flussratenimpulse zu vermeiden, da das gesamte mechanisch-fluidische System (inkl. der gerade fördernden Pumpe) vorgespannt ist, während die wieder befüllte, auf ihren Einsatz wartende Pumpe unter Atmosphärendruck steht. Verbindet man nun durch Schalten des 3/2-Wege Ventils diese wieder befüllte Pumpe mit der Applikation, findet ein Druckausgleich statt, der einen Ausgleichsstrom nach sich zieht. Folglich fließt ein gewisses Volumen von der bedruckten Applikation in die unbedruckte Pumpe. Die Flussrate in der Applikation wird dadurch gesenkt und kann im schlimmsten Falle sogar kurzzeitig negativ werden. Das gilt es zu vermeiden.
Abhilfe schaffen wir, indem wir den Druck der wieder befüllten Pumpe vor dem Hinzuschalten zur Applikation ebenfalls erhöhen, und zwar bis auf den selben Druck, der in der Applikation herrscht. Dies realisieren wir mittels zweier Druckmesser, mehrerer Ventile und einer intelligenten Software-Implementierung. Dabei wird die wieder befüllte Pumpe zunächst gegen geschlossene Ventile gefahren und dabei ein Druckvergleich der beiden Pumpen vorgenommen. Anhand der vom Anwender definierten Parameter wird dabei nach kurzer Zeit das Akzeptanzkriterium erreicht, bei welchem von einer Druckgleichheit ausgegangen wird und somit das Ventil zur Applikation geöffnet werden kann.
Da im Moment des Hinzuschaltens beide Drücke gleich sind, gibt es keinen Druckausgleich, somit auch keinen Volumenausgleichsstrom. Die Druck- und Volumenverhältnisse in der Applikation bleiben wie gewünscht konstant. Es entsteht ein kontinuierlicher pulsationsfreier Fluss (Conti Flow).
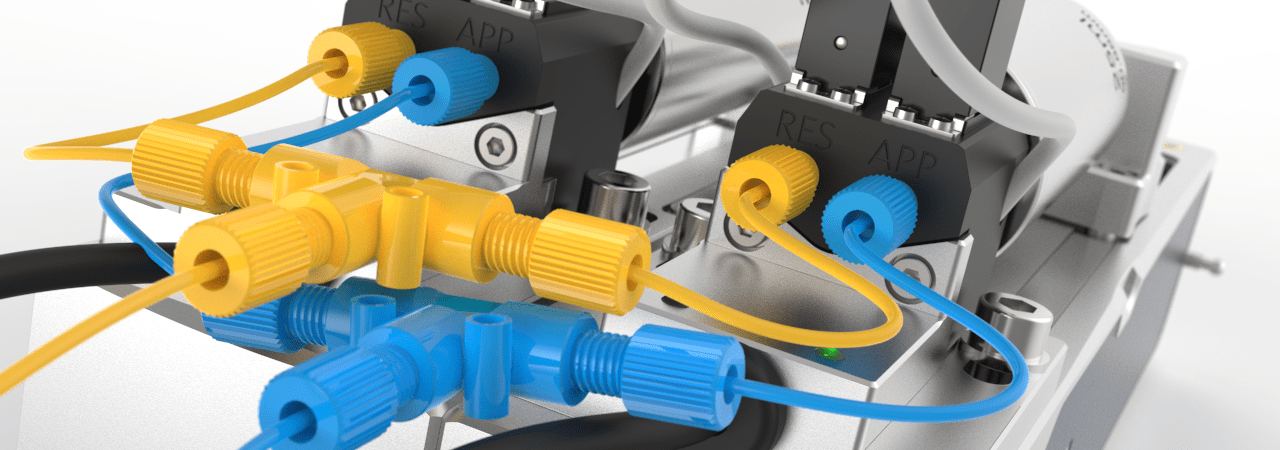
Die Realisierung dieses Prozesses mit einzelnen Hardware-Komponenten, wie Ventilen und Druckmessern, würde ein unübersichtliches System hervorbringen, das sich in erster Linie durch einen Wust an Kabeln und Schläuchen auszeichnet. CETONI steht nicht nur für zielführende konstruktive Lösungen, wir stehen auch für ansprechendes und innovatives Design. Deshalb haben wir speziell für Applikationen mit unseren Niederdruck- und Mitteldruckpumpen der Nemesys-Reihe ein äußerst kompaktes Modul entwickelt: Das Conti-Flow-Ventil. Es vereint alle beschriebenen Funktionalitäten auf kleinstem Raum, ersetzt eine Vielzahl der benötigten Schlauchverbindungen durch interne Kanäle, minimiert das Totvolumen der Applikation und ist dank unserer Software noch dazu äußerst einfach zu bedienen. Die Conti-Flow-Einheit ist Dank der verschiedenen Materialkombinationen, aus denen CETONI-Kunden wählen können, für unzählige Medien geeignet.